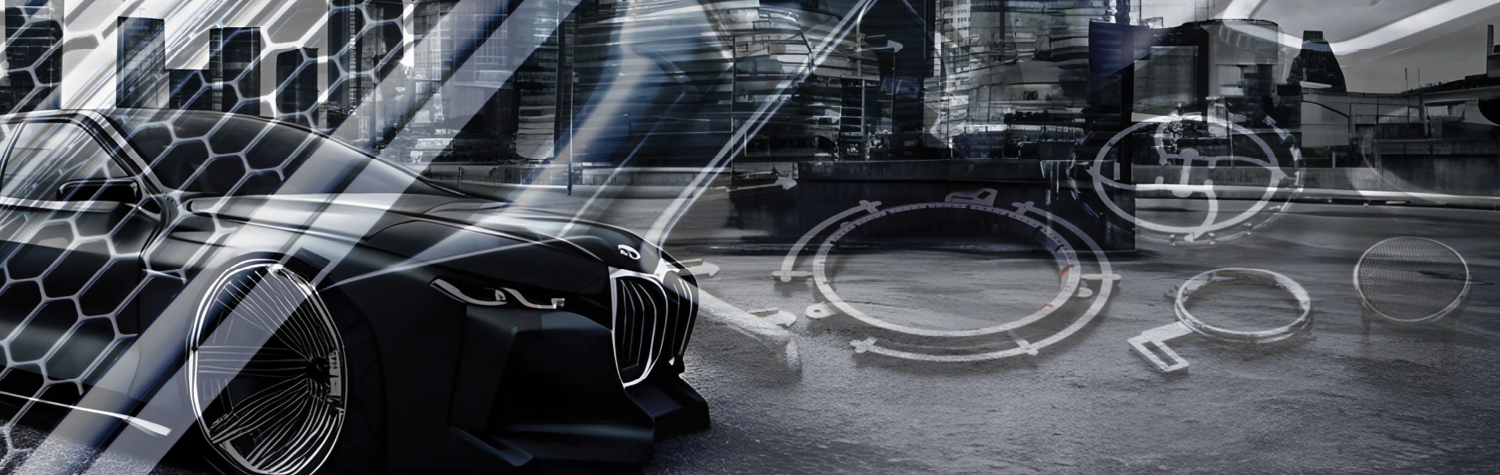
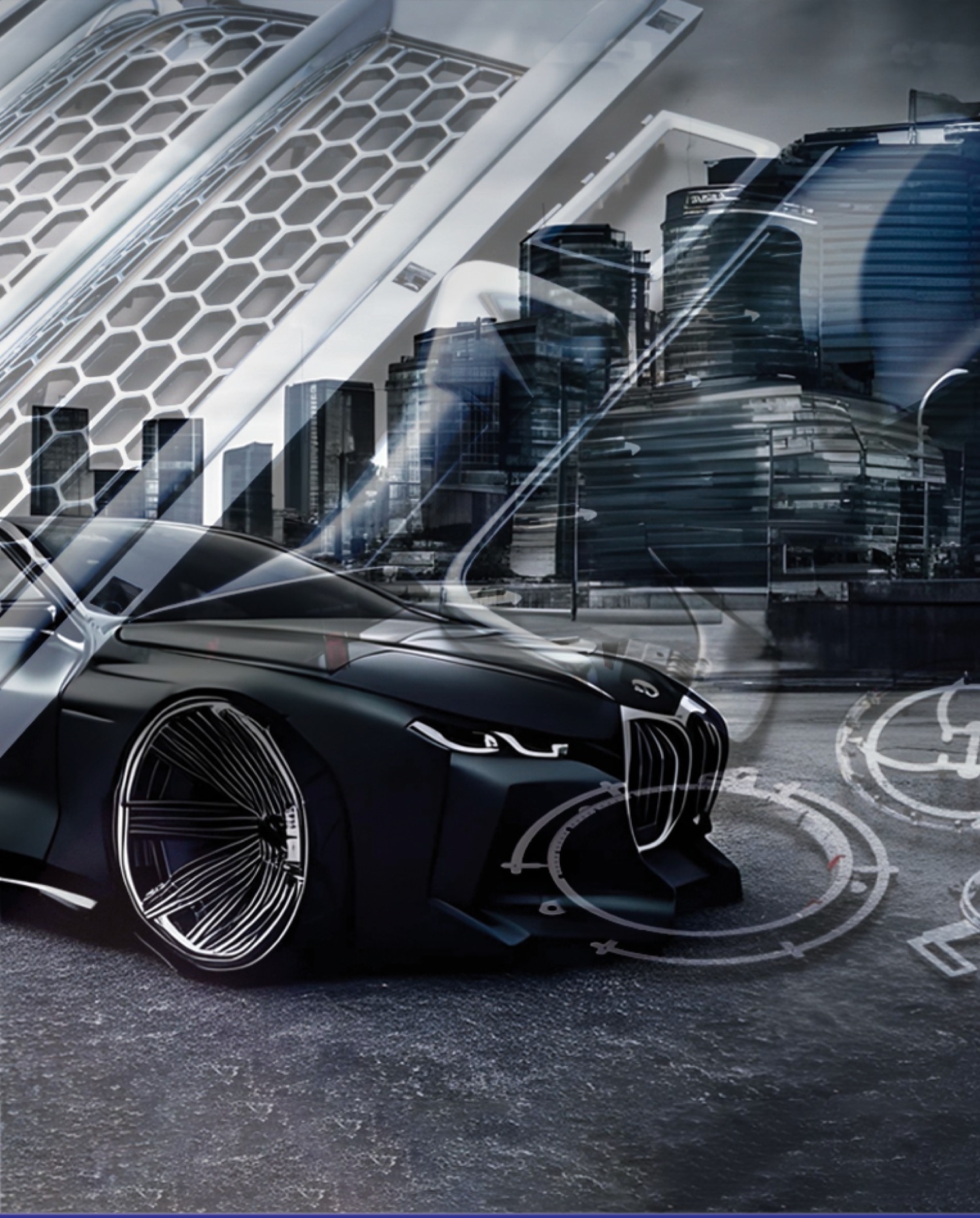
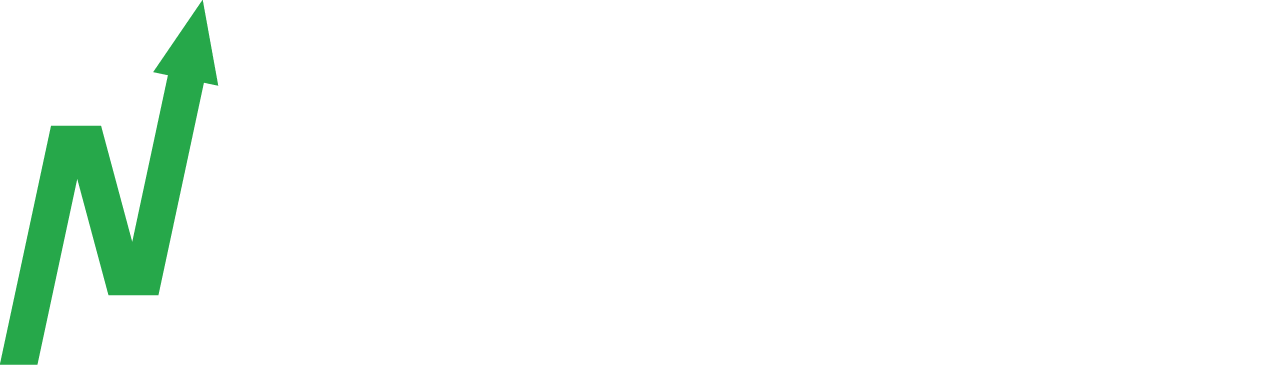
NEXT LEVEL IN DETAIL
塚田理研の最先端技術!
01
EU委員会
環境対応メタライゼーション
世界的な脱炭素の流れにより、製造業、中でも自動車産業を取り巻く環境は大きく変化しています。
特に、ヨーロッパでは、自動車の車両設計から生産、廃車までの全過程における『資源循環性の向上』を担保するため、様々な法令が制定されております。
塚田理研工業では、常にプラスチックめっきの最先端、画期的かつ、サステイナブルなソリューションを編み出し続けていることで、ヨーロッパのような厳しい環境基準にも準拠しためっき技術の提供が可能です。
ヨーロッパの動向
欧州委員会は、2023年7月に「自動車の循環設計とELV(End of LifeVehicles)管理規則」(案)を発表しました。
これは、2000年に制定した、廃車(End of Life Vehicles=ELV)を環境に配慮した方法で処理することや、新車に使用される有害物質の制限、再使用率、リサイクル率、エネルギーリカバリー率を設定した「ELV指令」と、2005年に採択された自動車の型式認証プロセスの紐付けを可能とする「自動車型式認証における再使用、再利用、再生の可能性に関する指令(3R型式認証指令)」を1つにまとめ規則化する案です。
上記2点の法令下で、ELVの回収や車両に使用する有害物質の低減、廃車からの原材料リサイクル率が進んだ一方、廃車から出る金属廃棄物の分別と価値化や、プラスチック、電子部品、複合材料のリサイクル率が非常に低いことが問題視され、2023年の「自動車の循環設計とELV(End of Life Vehicles)管理規則」(案)が発表されました。
「自動車の循環設計とELV(End of Life Vehicles)管理規則」(案)では、現行法令での課題に対処するため、以下6点を挙げています。
1)循環設計:
設計と生産の循環性を高め、容易な解体をデザインする。設計段階より、容易な解体・取り替えを意識し、解体業者に解体方法の情報を提供する。
2)リサイクルパーツの使用:
新車に使用するプラスチックのうち、25%をリサイクル素材、その内25%を廃自動車由来のものとする。
3)より良い処理:
より多く、良い品質の良い原材料(重要原材料、プラスチック、鉄、アルミなど)を回収、再生材を増産する。廃自動車からのプラスチックの30%をリサイクルする。
4)より良いガバナンス:
「拡大生産者責任(Extended Producer Responsibility:ERP)」制度を導入し、生産者責任を強化。廃棄物処理事業に適切な資金提供を行うことで、リサイクル業者に廃車由来のリサイクル材料の品質向上のインセンティブを与え、結果、生産者とリサイクル業者の協力関係を強化する。
5)より多く、よりスマートに回収:
解体業者などへの廃自動車の確認・報告義務と解体証明書の発行、税関との情報共有による第三国への違法輸出抑制、廃自動車の拘束力ある定義の再設定などにより、回収率を改善する。
6)より多くの車両を対象に:
現行のELV指令の対象外であるトラック、バス、トレーラーに対する一連の最低限の処理要件を導入し、段階的に対象車両を増やしていく。
塚田理研の6価クロムフリーの
めっき技術
2000年制定のELV指令で、有害物質として新車への使用を禁止された6価クロームは、これまでその見た目と機能性の高さにより、非常に多くの製品に使用されてきました。
塚田理研では、プラスチックにめっきをする際、エッチング工程と電気めっき工程の2段階で使用されてきた6価クロームをどちらの工程でも使用せず、同等の見た目と機能性を実現するクロムフリー工法を開発し、量産が可能となっております。
マンガン、UV、オゾンなど、6価クロムを使用しない多彩な表面改質技術を持ち、エンプラやスーパーエンプラを含む様々なプラスチックにクロムフリーめっきを施す技術と量産体制を持ち合わせております。
廃車由来のプラスチックのクローズドループリサイクルをする技術
自動車の循環設計とELV(End of Life Vehicles)管理規則」(案)では、廃車由来のプラスチックのリサイクル率の低さを改善するため、「新車生産に必要なプラスチックのうち、25%以上にリサイクルプラスチック、さらに、そのうち25%が廃車由来のもの」と定めています。
塚田理研では、廃車から出た樹脂めっき製品を再度樹脂と金属に戻し、原材料としてバージン材と混ぜ(開発中)、成形&めっきし、新車に戻すクローズドループリサイクル(CLR)体制を確立中です。 このCLRを経て実現した新車パーツは、それを使用するだけで、上記基準値の達成が可能となり、最終製品のLCA(ライフサイクルアセスメント)評価を高めることに貢献します。
低環境負荷カーボン入りPA材「Kobatron」と「Kobatron」へのめっき
「Kobatron」は、塚田理研のパートナー企業、富士加飾(株)が開発したrCF(recycled Carbon Fiber)と、リサイクルPAをコンパウンドし、ペレット化した製品です。 CFを長繊維にリサイクル(rCF)し、廃漁網からリサイクルしたPAとコンパウンドしたもので、CFのバージン材を利用したものと比べ、格段にCO2排出量が少なく、LCA(Life Cycle Assessment)評価が高い、低環境負荷製品となっています。
塚田理研では「Kobatron」成型品への高密着なめっきを施す特殊工法を開発進行中。また、「Kobatron」の販売も対応可能です。
02
廃車由来のプラスチックのクローズドループリサイクル(CLR)
新車におけるリサイクルプラスチック構成基準
前述の「自動車の循環設計とELV(End of Life Vehicles)管理規則」(案)では、新車生産に必要なプラスチックのうち、25%以上にリサイクルプラスチック、さらにそのうち25%が廃車由来のものという基準が挙げられました。
塚田理研では、この基準値の達成と、上記規則(案)が真の目的とするサーキュラーエコノミーを実現するため、大きく2種類のアプローチをとっています。
- 1.
- 廃車由来のプラスチックや金属を確実に新車製造に利用するためのクローズドループリサイクル(CLR)体制の確立。
- 2.
- 強度や品質の担保が可能なリサイクルプラスチックとバージン材を混ぜた材、及び、それに対する高密着めっきの開発。
塚田理研のクローズドループ
リサイクル(CLR)体制
塚田理研では既に、不良品などのめっき済み製品を金属と樹脂に分離し、それぞれを100%有価物としてリサイクル可能な体制(カスケードリサイクル)を確立しています。現在、このリサイクルスキームをさらに高め、CLR(クローズドループリサイクル)体制を確立し、サーキュラーエコノミーを実現するべく様々な国内パートナー企業様と実証実験を進めております。
廃車由来の樹脂めっき製品を再度樹脂と金属に戻し、原材料としてバージン材と混ぜ、成形&めっきし、新車に戻すクローズドループリサイクル(CLR)を経たパーツは、高いLCA(ライフサイクルアセスメント)評価をえることができ、最終製品のLCA評価にも大きく貢献することが可能です。
LCA(Life Cycle Assessment)について
LCA(Life Cycle Assessment)とは、製品やサービスのライフサイクル全体(原材料の生産、製品の製造、輸送、販売、使用、廃棄、再利用等)の環境負荷を評価する手法のことです。
例えば、自動車業界の場合、燃費など一部の環境負荷指標を見るのではなく、LCAを用い、自動車の原料調達、生産、使用、廃棄、リサイクルまでのすべてのプロセスにおけるエネルギー消費、二酸化炭素排出量などを推定し、自動車の全寿命における環境への負荷を評価し、対策することが求められています。
塚田理研が国内で確立中であるクローズドループリサイクル体制の元生産した廃車由来のリサイクルプラスチック配合樹脂めっき製品は、特に原材料の調達といった環境負荷を低く抑えられることで、高いLCA評価を担保します。結果、それらを使用した新車のリサイクル基準値やLCA評価向上に貢献することが可能です。
03
リサイクルカーボンへのメタライジング
CFRP(Carbon Fiber Reinforced Plastics=「炭素繊維で強化されたプラスチック」)は、その軽さや強度などから、自動車・バイク業界、航空宇宙業界、スポーツ、医療、建築などさまざまな用途と需要があり、活用されています。
しかし、世界的な脱炭素の流れの中においても、CF(炭素繊維)のリサイクル技術は依然不十分で、バージン材と比べ、強度が弱く、価格が高いという現実的に採用不可能なrCF(recycled Carbon Fiber)しかありませんでした。
高性能なrCF
(recycled Carbon Fiber)
様々な分野で活用されているCFRPですが、使用済みのCFRPからCF(炭素繊維)とプラスチックを分離し、それぞれをリサイクルすることへの困難さから、これまで大部分が埋め立て処理されてきました。
従来のリサイクル技術では、CFRPから、炭素繊維(CF)を回収する際、毛羽立ちや粉末の発生などの問題があり、リサイクルした炭素繊維(rCF)の繊維強度は、バージン材と比べ60~80%程度でした。これでは、プラスチックを強化するための補強材として信頼性が低すぎる上、コストもバージン材より高いため、rCFを使用したCFRPの実現に至りませんでした。
この度、塚田理研のパートナー企業の富士加飾(株)が開発したリサイクル技術により、強度がバージン材と遜色なく、価格が10~20%削減できるrCF(recycled Carbon Fiber)が実現しました。 このrCFを使用し、リサイクルプラスチックとコンパウンドした材に、塚田理研の高密着なめっきを施すことで、脱炭素に大きく貢献し、LCA評価の高い製品提供が可能といえます。
rCFのLCA
今回のrCFで強化された樹脂が、通常のCFRP(バージン材)や他の材と比べ、どれくらいの環境負荷があるのかを一見できるよう一覧にしてみました。
現時点でのrCF樹脂のLCA評価は、2.5(今後さらに下がります)KgCO2/Kgとなり、CFRPのバージン材と比べると環境負荷が、約1/10近くとなっています。 通常、これらの材に対し、1次・2次加工などが施され、それぞれのタイミングでもCO2排出量に差が開くため、rCFを使用した樹脂を用いた最終製品と通常のCFRP(バージン材)では、LCA評価にさらに大きな差が出ると言えます。
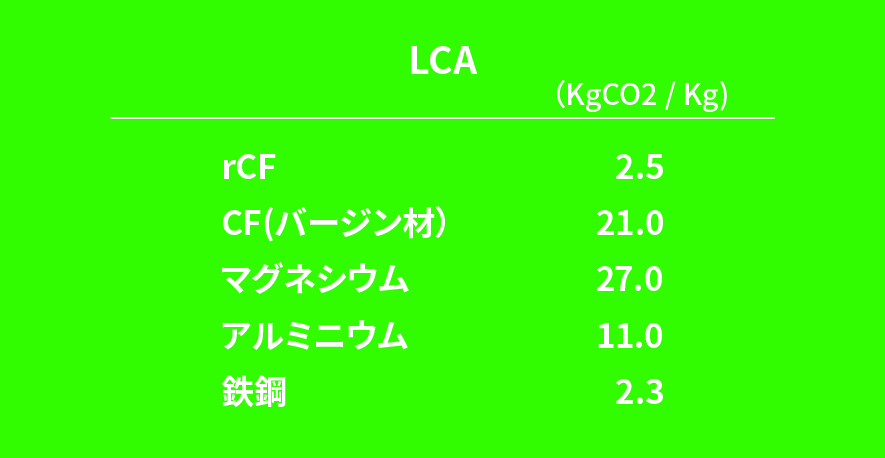
04
従来工法でのPPSへのウェットプロセスメタライジング
脱炭素の潮流の中、軽量化を目的とし、金属を樹脂で代替するものとしてスーパーエンジニアリングプラスチック(以後、スーパーエンプラ)が着目されていました。
しかし、スーパーエンプラは、通常の方法でめっきを付けられず、金属を代替するための電磁波シールド性が付与しにくいという問題がありました。
そこで、塚田理研は、DIC株式会社と吉野電化工業株式会社と共同で特殊な処理なくめっき可能な、PPS(スーパーエンプラ)コンパウンド「DIC.PPS MP-6060 BLACK」(以下「MP-6060」)を世界初に開発しました。
特殊な処理不要、既存の設備で
めっき可能な
【PPS - MP-6060】
PPSはスーパーエンプラとしての耐久性や軽量化、加工性などの長所から、車載電子機器などに使用されてきました。これらの機器には、電磁波シールド性を持たせるため、めっきが必要不可欠です。
しかし、これまでPPSはその高い耐薬品性から一般的なプラスチックめっきで用いられるエッチング溶液が前処理に使用できず、めっき密着性を付与するために「ブラスト処理」、「プラズマ処理」、「フッ酸処理」、「濃硝酸処理」などの特殊なエッチング工程が必要でした。
この度、開発したMP-6060は、汎用溶液でのケミカルエッチングとWPM(ウェットプロセスメタライジング)により、既存のプラスチックめっき設備でスーパーエンプラへの金属めっきが可能となりました。